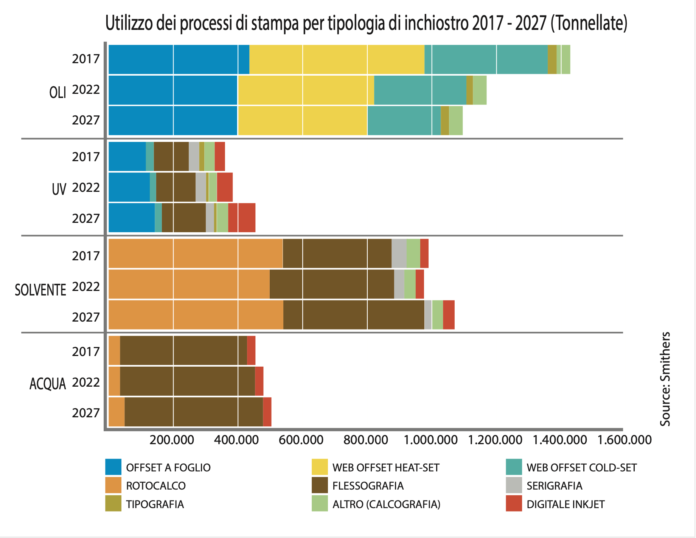
Negli ultimi anni si è verificato un deciso ricambio di attrezzature per la stampa offset, il parco macchine si è svecchiato. Questo può essere il punto di partenza su cui avviare un ragionamento virtuoso in ottica di risparmio energetico e basso impatto ambientale.
Il processo di transizione energetica che sta permeando tutti i settori della vita pubblica e privata è baricentro per l’attenzione di tutti. Strettamente derivato dalla crescente consapevolezza che il nostro pianeta sta facendo indigestione di gas serra (Green house gas, GHG), principalmente CO2, che provocano il riscaldamento globale. Indigestione, perché i gas serra (oltre alla CO2 anche il vapore acqueo H2O, il metano CH4, l’ozono O3, lo sono) hanno superato il limite per mantenere in equilibrio l’atmosfera del nostro pianeta, che, senza i quali, sarebbe parecchio inospitale, con una temperatura media di -18°. “Paradiso per gli sciatori”, ma un tantino difficile da riscaldare e del tutto invivibile. La cosiddetta carbon footprint è quindi diventata un metro di valutazione delle attività umane al pari oserei dire degli altri parametri tradizionali, produttività, redditività, efficienza, eticità. Potrebbe in futuro entrare come parte del modello organizzativo aziendale ai sensi del D.Lgs. 231/2001?
Vale la pena ragionare quindi su quale può essere l’impatto ambientale della stampa. Può uno stampatore offset contenere la propria impronta ambientale e intraprendere una rotta virtuosa verso la carbon-neutrality? Va considerato per onestà intellettuale che oggi non stiamo vivendo un’epoca in cui la stampa offset, soprattutto legata a prodotti commerciali ed editoriali si può definire florida e in marcata crescita. Parlare quindi di problemi legati all’ambiente a imprenditori che devono fare i conti a fine mese con una redditività che può scricchiolare, potrebbe sembrare fuori luogo. È altresì vero che negli ultimi anni si è verificato un deciso ricambio di attrezzature per la stampa offset, il parco macchine si è svecchiato decisamente, e per tale motivo rappresenta un’opportunità per avviare un ragionamento virtuoso.
Tutti i produttori dichiarano oggi il loro impegno nella riduzione dei consumi energetici con l’obiettivo di ottenere la cosiddetta carbon-neutrality. Sicuramente rispetto al passato grandi passi in avanti sono stati compiuti dal 1997, quando a Kyoto fu stipulato il protocollo internazionale per il contenimento delle emissioni. Interessante in questo senso il dato che fornisce sia Heidelberg che Komori relativo alla riduzione del 40% dell’energia consumata per stampare 1000 fogli da un impianto odierno (Heidelberg) rispetto a uno del 1990 o semplicemente paragonando la stessa produzione realizzata con diversi vecchi impianti contro la medesima ottenuta con un impianto nuovo (Komori). Tradotto in cifre, se i dati sono corretti, ogni 1000 fogli, alle tariffe attuali dell’energia, corrisponderebbe un risparmio intorno ai 2 euro. Moltiplicato per le copie stampate in un anno, i numeri che appaiono potrebbero divenire interessanti per considerare il ricambio di attrezzature di generazioni più energivore.
Risparmio energetico, cosa fare
Per analizzare come le moderne macchine da stampa possono essere progettate per risultare più rispettose dell’ambiante ho realizzato una piacevole chiacchierata con l’ingegnere Peter Andrich, amministratore delegato di Koenig&Bauer IT e Massimo Brescianini, responsabile tecnico di Koenig&Bauer IT.
Prima di entrare nel vivo delle considerazioni emerse, vorrei però analizzare il processo offset per identificarne alcune caratteristiche peculiari che impattano sulla prestazione energetica complessiva. La stampa offset usa lastre di alluminio che vengono inchiostrate con inchiostri a base di solventi, oli minerali o vegetali, acqua o per polimerizzazione (UV). Questi inchiostri necessitano di aria calda, radiazione infrarossa, lampade UV per trasformarsi in residuo secco sul supporto. Le stesse lastre offset richiedono un processo fotografico per essere impressionate e sovente, un processo più o meno ricco di prodotti chimici per il trattamento successivo (sviluppo). Sul versante del trattamento lastra sono stati fatti in questi anni, passi avanti importanti, come la riduzione dei prodotti chimici coinvolti nel trattamento (lastre low-chem) o l’eliminazione dell’intera linea di sviluppo (lastre process-less). Si può quindi affermare che dal punto di vista della preparazione della matrice di stampa, oggi esiste la possibilità di ridurre al minimo il consumo energetico legato a una parte del processo che non conferisce nulla in termini di valore al prodotto finito ma è un sottoprocesso, per quanto indispensabile, che dà in esito un rifiuto da trattare. La tecnologia delle lastre e dei CTP credo ormai sia arrivata a un punto di maturità per cui non potremo attenderci significativi passi in avanti in termini di impatto ambientale, se non sostituendo le lastre attuali con altri materiali o con matrici completamente digitali a scarto zero. Timidi tentativi già fatti in passato, che non hanno dato ancora i risultati sperati.
Tornando sugli inchiostri offset e la loro asciugatura, quello che oggi le moderne macchine attuano è un controllo il più possibile accurato del calore prodotto per l’essiccazione, evitando ogni spreco e utilizzando a pieno l’energia prodotta. Come nel caso del sistema VariDryBlue che propone Koenig&Bauer, dove la produzione di aria calda è ottimizzata e resa efficiente mediante il recupero della stessa dai condotti di scarico. L’aria calda, quindi, non viene buttata via ma rimessa in circolo per il riutilizzo. Naturalmente questo impianto necessita di apparati aggiuntivi nella struttura della macchina che si traducono in costi di acquisto aggiuntivi. Il ritorno dell’investimento extra è però veloce e probabilmente conveniente pensando al beneficio in termini di costi energetici e di conseguenza ambientale. Infatti, l’essiccazione dell’inchiostro è il sottoprocesso della stampa più energivoro e per tanto attuare un risparmio in quella fase, incide parecchio sul bilancio energetico finale. La soluzione proposta da Koenig&Bauer è esclusiva, ma ovviamente tutti i brand stanno operando miglioramenti in questo senso, ottimizzando l’uso dell’energia in funzione del prodotto da stampare, in termini di dimensioni del foglio e copertura di inchiostro. Se l’asciugatura è un punto centrale, anche il risparmio di carta è una leva che impatta sul bilancio energetico del processo. Poter risparmiare la carta che viene refilata e quindi non finisce nel prodotto finito ma nel cassone della carta stampata da riciclare è senz’altro qualcosa che si aggiunge al processo virtuoso di salvaguardia degli sprechi. Come ad esempio Koenig&Bauer che ha operato un passo in avanti introducendo nel proprio sistema di controllo colore una striscia più stretta, che riduce lo spazio necessario per la lettura delle patches. Possono sembrare piccolezze, ma se si entra in una forma mentis dove ogni elemento, ogni atto, ha un suo impatto nella produzione di gas effetto serra, allora non va tralasciato alcun dettaglio. Tanto più che alcuni risparmi sono a costo zero, come questo. Mi viene spontaneo fare un parallelo con ciò che avviene nelle competizioni di Formula Uno; è la somma di millesimi di secondo, risparmiati qua e là, a fare il tempo migliore sul giro.
Sul risparmio energetico impatta anche un altro fattore: i tempi di avviamento. La macchina da stampa quando è accesa consuma corrente. Per questo motivo nei momenti di inattività su alcune attuali macchine esiste un pulsante di messa in pausa (II) che diminuisce il consumo staccando certi apparati o attenuandone l’assorbimento (Heidelberg). Ma durante le procedure di avviamento il tempo è il fattore determinante. Per tanti motivi, e anche sul piano del risparmio energetico. Poter fare un avviamento in soli 5/6 minuti riduce i consumi. Questo è possibile per esempio mediante il sistema di Koenig&Bauer che simultaneamente unisce il lavaggio dei caucciù con la sostituzione della singola lastra. Che si inserisce nella filosofia delle moderne macchine da stampa, che, sfruttando automazione, le machine learning technologies e intelligenza artificiale, permettono di operare secondo una logica di continuità produttiva “push to stop”. Ottimizzare i tempi di avviamento riducendo consumi e conseguentemente costi, rende il processo offset ancor più competitivo sulle basse tirature. È veramente interessante osservare come alla crescita delle prestazioni delle tecnologie digitali di stampa, sempre più veloci, qualitative e versatili in termini di gamma di supporti, risponde la stampa offset a foglio di ultima generazione, che come tecnologia ormai matura, lima tutte le imperfezioni, scovando gli ultimi spiragli di efficientamento.
C’è un aspetto molto interessante in tema di risparmio energetico nella macchina da stampa offset che Koenig&Bauer ha introdotto come novità in via sperimentale in due aziende pilota in Germania e che sta fornendo ora dei dati di ritorno dopo il primo anno di impiego. Si tratta di un monitoraggio capillare dei vari dispositivi della macchina, attraverso una serie di sensori che rilevano il consumo istantaneo di energia, rapportato alla produzione (ad esempio KWh/1000 fogli). Distribuendo questi sensori nei vari apparati della macchina e monitorando questi con un’APP, è possibile tracciare per ogni commessa di lavoro, qual è l’impatto sui consumi. Pensandoci, questo apre diversi scenari, perché rende possibile utilizzare i feedback elaborati per modificare procedure di lavoro, cambiare materie prime, ottimizzare le offerte economiche, pianificare le produzioni. Ad esempio scoprendo come impatta ogni singolo gruppo stampa sui consumi, si possono avere dati consuntivi estremamente precisi che possono pilotare nuove azioni commerciali. Lo stesso si può dire per i caucciù e così per le diverse carte e inchiostri. Questo equivale a affermare che il costo orario della macchina da stampa non è più un valore più o meno costante che dipende dai fattori tecnici del prodotto da realizzare, ma un algoritmo arricchito da una componente analitica che tiene in considerazione anche del reale consumo energetico in tempo reale della macchina mentre sta producendo la commessa. Una soluzione che evidentemente è ritenuta un elemento importante dai costruttori dato che anche Heidelberg nei prossimi mesi dovrebbe rendere disponibile questo tipo di monitoraggio della macchina (in Germana inizialmente). È interessante sottolineare che secondo i dati pubblicati da Heidelberg, la maggior efficienza energetica la si ha utilizzando la macchina alla massima velocità. Il che risulta evidente se si considera l’unità di misura e cioè KWh/1000 fogli, dato che la macchina impiega meno tempo per concludere la tiratura. Risparmiando tempo anche sul cambio lavoro, l’efficienza cresce ulteriormente.
Inchiostri e materiali
Allargando un po’ il ragionamento all’intera filiera produttiva della stampa offset e cioè considerando i concetti base dell’economia circolare, che ci induce a privilegiare il consumo di materie prime a basso impatto ambientale, lo stampatore dovrebbe interrogarsi anche in merito alla provenienza di inchiostri e carte e tutte le materie prime che impiega nella produzione. Se questi prodotti anziché provenire da siti produttivi posti a pochi chilometri, per arrivare nello stabilimento di stampa devono compiere viaggi attraversando continenti, certo consumano più risorse producendo molta più CO2. Oppure se i prodotti devono viaggiare per via aerea piuttosto che per nave o treno, certamente sono più voraci in termini di energia.
Certamente la situazione drammatica del clima planetario ci impone una presa di coscienza e di conseguenza un impegno e attenzione nuovo rispetto alle scelte. Nel 2013 il Technical Committee TC130 di ISO ha pubblicato lo standard “ISO 16759:2013 Graphic technology — Quantification and communication for calculating the carbon footprint of print media products”, nel 2022 Intergraf ha pubblicato la roadmap per il calcolo, la riduzione e la compensazione della CO2 nell’industria della stampa, un framework, che accogliendo lo standard ISO, indica una procedura per l’assesment generale della carbon footprint aziendale e la ricerca dei punti sensibili di miglioramento. Gli strumenti operativi ci sono, tutti gli attori della filiera devono interpretare la propria parte.