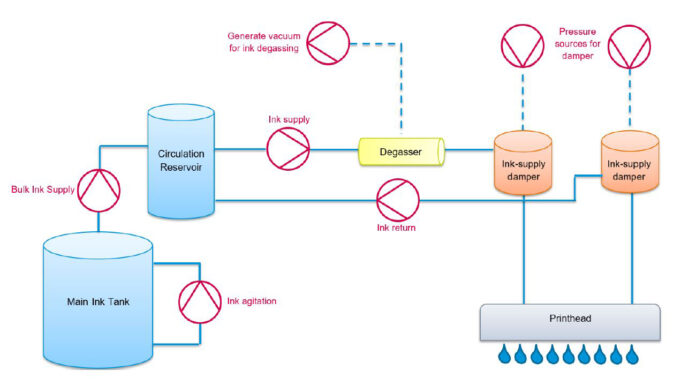
La progressiva introduzione dei sistemi di stampa inkjet nel mondo commerciale e packaging a foglio porta con sé nuovi parametri tecnologici e nuove unità di misura. Sono sufficienti per poter descrivere la rappresentazione visiva dello stampato? Servono a farci capire se la tecnologia che stiamo valutando è centrata sulle esigenze di produzione che abbiamo individuato?
Se utilizziamo l’ottica dello stampatore i termini di valutazione di un sistema di stampa sono l’uso dello stampato, il tipo di produzione, la qualità attesa, i processi di lavorazione; le risposte a queste domande arrivano dai dati relativi alle tecnologie di stampa digitale, correttamente collocati nel proprio schema di analisi e interpretati incrociando altri parametri. L’analisi di un sistema di stampa inkjet fornisce numerosi dati di cui alcuni, come quelli relativi alle teste di stampa, sono di difficile comprensione e applicazione.
Le teste di stampa inkjet sono il risultato della ricerca di molteplici discipline come la scienza dei materiali, fluidodinamica, acustica, balistica. Esistono diversi modelli di teste di stampa che rispondono a diverse applicazioni e la stampa commerciale e packaging è solo l’ultimo dei settori a esserne stato interessato: sistemi di codifica, deposito di fluidi funzionali, ceramica, vetro, sinterizzazione, stampa 3D, tessile, transazionale, largo formato sono alcuni dei settori industriali che utilizzano teste inkjet in ambito produttivo. In molti casi le teste sono le stesse e, oltre al fluido che le attraversa, cambiano solo le logiche di gestione, il numero e la dimensioni dei nozzle (ugelli) di stampa, la frequenza di emissione. Per questo motivo è bene definire il campo di applicazione e considerare solo i dati che interessano il settore della stampa commerciale e packaging: dimensione delle teste, la densità e dimensione dei nozzle, il sistema e frequenza di espulsione, la temperatura di lavoro, il sistema di gestione dell’inchiostro.
Dimensione delle teste
La dimensione della testa di stampa incide in modo diretto sull’area di stampa coperta e quindi, in base alla dimensione e densità dei nozzle, la risoluzione nativa di stampa.
La rilevanza della dimensione della testa è visibile nei sistemi di stampa digitale multipass (stampanti largo formato flatbed o roll to roll) perché determina quanti passi devono essere compiuti per raggiungere, ad esempio, la risoluzione desiderata; spesso sono montate più teste per poter aumentare la velocità di produzione a parità di risoluzione. Nelle macchine single pass le teste sono montate in array (linea) per poter coprire l’area di stampa e ogni array gestisce un colore di stampa.
Ci sono vari modi di costruire gli array e la logica di controllo di questi gioca un ruolo determinate in due aspetti tecnici fondamentali per la produzione: il recupero della manca emissione (jet-out) e il mantenimento dell’allineamento. Nel disegno degli array ci sono delle aree di sovrapposizione tra le teste che possono generare il fenomeno del “overlapping”, ovvero una riga più scura nella direzione di stampa dovuta a una ridondanza di getto nello stesso punto, e per questo ci vuole un controllo specifico nell’allineamento.
Dimensione e densità dei nozzle (ugelli)
La piastra di emissione è la parte “visibile” della testa. I fori sono generalmente realizzati con sistemi laser che realizzano un cono di emissione la cui dimensione finale determina la dimensione della singola goccia. La densità è determinata dalla dimensione della piastra e dal numero di fori di uscita, andando a determinare la risoluzione nativa della testa espressa in npi (nozzle per inch). Questo è uno dei dati che fornisce una informazione dettagliata sulla risoluzione ma non esaustiva per lo stampatore, in quanto il risultato visivo finale è dato dalla combinazione della risoluzione nativa, dal numero di emissioni consecutive (single drop o multidrop) e dalla dimensione finale della goccia sul supporto.
Le linee di nozzle sulla singola testa variano in base al disegno dei costruttori e possono essere e sono a 2 o 4 file in base al campo di applicazione e il numero d’inchiostri che devono essere stampati. Questo è il motivo perché su alcuni stampanti largo formato ci possono essere sensibili velocità differenti in base al numero dei colori oltre quadricromia, mentre nelle macchine da produzione single pass ogni array è dedicato ad un colore.
La dimensione e la forma del nozzle è determinate per mantenere costante la forma della goccia emessa, la dimensione massima della componente solida dell’inchiostro, l’energia necessaria per l’espulsione della goccia. L’usura del nozzle è visibile solo al microscopio ma i suoi effetti in stampa sono evidenti perché provocano una alterazione della stesura del “retino” di gocce con effetti di “microspray” attorno alla goccia, microdensità differenti (effetto rumore), slabbrature nei dettagli. Anche questi effetti non sono determinabili solamente dalla costruzione della testa di stampa ma combinati con il tipo di inchiostro utilizzato che può determinare un tempo di usura differente.
I fattori che influenzano l’espulsione (sistema, frequenza, viscosità, temperatura)
L’espulsione delle gocce è il momento su cui si concentra tutta l’attività della testa di stampa ed è caratterizzato dal modo (continuo o su richiesta) e dal metodo (pistone, termico, piezo). La scelta del tipo d’inchiostro utilizzabile (dal punto di vista del produttore di teste) è determinata principalmente da questi fattori, a cui si collegano altri più tecnici e rilevanti nelle scelte compiute dagli sviluppatori e produttori.
La frequenza di emissione è determinante per la effettiva velocità di produzione mantenendo costante l’emissione e la “spinta” di emissione delle gocce durante l’intero ciclo produttivo. L’effetto di questo fattore è impattante nella stampa digitale a bobina nel rapporto velocità/risoluzione, e determina a quale velocità massima potrà andare una macchina ibrida a seconda se il gruppo digitale deve stampare uno o più colori. La frequenza determina anche la composizione degli inchiostri sia per la dimensione delle parti solide sia per la viscosità: l’inchiostro entra nella camera di compressione perché richiamato dopo l’espulsione o perché spinto dal sistema di pompaggio ed affinché l’afflusso sia continuo e l’espulsione costante la viscosità deve rimanere fissa. Per questo fattori compromettenti come la variazione di temperatura e la miscelazione dei compenti degli inchiostri siano sempre sotto controllo utilizzando sistemi di pompaggio e afflusso adeguati. Dato che alcuni inchiostri possono formare più depositi di altri, le teste a più alta risoluzione (che hanno nozzle più fini e più densi) sono costruite con un sistema di ricircolo che mantiene in agitazione costante l’inchiostro evitando che le parti solide e gli additivi si concentrino in modo anomalo nel foro di espulsione.
Quale manutenzione
La vita di una testa di stampa si misura un numero di gocce o litri che emette prima di dover essere sostituta, con un fattore di incidenza significativo quando si stampa sulle macchine a bobina, meno sulle macchine a foglio e largo formato dove il rischio di sostituzione è più collegato ad eventi accidentali. Nell’arco di questa vita le teste lavorano sempre in alta efficienza e le operazioni di manutenzioni sono per lo più pulizia dei residui d’inchiostro sia sulla piastra sia nelle camere.
L’espulsione dell’inchiostro resta comunque una operazione meccanica per cui l’ispezione per il controllo dell’emissione della goccia è sempre post-comando. Sono adottati diversi metodi di controllo per poter identificare il problema in tempo reale come l’analisi della variazione di pressione in camere di espulsione, il controllo dei segnali elettrici dei singoli nozzle, la lettura laser o stroboscopica dei getti, la scansione post stampa; lo scopo è di comunicare in tempo reale con le teste e attivare i nozzle di compensazione o le procedure di spurgo e pulizia. La teste inkjet industriali attualmente sul mercato hanno una capacità di produzione elevata, adeguata alle esigenze del comparto stampa commerciale, packaging e largo formato, e la crescita è sempre più il risultato di un combinato con inchiostri e materiali.
Quello che deve essere chiaro allo stampatore che vuole approfondire l’argomento sono i risultati produttivi attesi e i costi stimati, considerando che le teste, proprio perché sono il motore di tutta la stampa inkjet, si possono usurare e possono essere sostituite, altri due dati utili da approfondire con i fornitori.